If you need a heat exchanger that can handle liquids with high solids or fiber content without blocking the fluid passages, plate heat exchangers are unsurpassed for their small size.
These units are also easier to maintain and clean than shell-and-tube heat exchangers. They’re also less expensive to purchase than new equipment.
Flexibility
Plate and frame heat exchangers use gasket plates arranged in a frame-like structure to separate the hot and cold fluids. The corrugated patterns of the plates enhance turbulence, allowing for more excellent heat transfer between the two fluids.
These compact units require less space than shell and tube heat exchangers to achieve similar temperature approaches, and they can be operated under either cross-flow or counter-flow conditions.
With a simple modification to the unit, you can expand its capacity as production needs change. To do this, bolt-on longer carrying and bottom bars and install more plates. However, doing this only as necessary is important because too many plates will reduce velocity and turbulence. This can lead to the formation of fouling pockets. This is called “plate fouling” and can dramatically lower efficiency.
Less Expensive
As the name implies, plate heat exchangers are less expensive than shell-and-tube designs. They also have superior heat transfer ability and require less space for the same volume of liquids.
As your production requirements change, it is possible to increase the capacity of a plate heat exchanger by adding longer carrying and bottom bars. However, it’s essential to add the new bars only as necessary. Over-sizing an exchanger decreases the plate’s turbulence and velocity, increasing the likelihood of plate fouling.
Plate and frame rental from a trusted supplier is the safest way to ensure you use up-to-date equipment with the latest technology. With an annual rental agreement, you can always have the best and safest plate heat exchangers for your process.
Ease of Maintenance
High-quality plate and frame heat exchangers can operate efficiently for up to ten years without maintenance. They are also easier to clean than shell-and-tube models. This is particularly true when handling liquids with high solids or fiber content that tend to clog the fluid passages in larger shell-and-tube units.
Plate and frame heat exchangers are gasketed or welded together. They can be expanded by adding more plates if heating or cooling needs change. The tightening of the tie-bars is done to a plate dimension rather than a torque specification, which helps prevent leaks.
Reliability
Plate heat exchangers are unsurpassed for their high levels of thermal efficiency. They also have a shallow risk of clogging due to solids or fibers that collect in the fluid passages and block the plates’ surface areas.
They can be cleaned in place or taken apart to be inspected and cleaned. This means they are more reliable than shell-and-tube models, which require more upkeep and can be more challenging to access internally.
Another reason to choose a plate-and-frame heat exchanger is its modularity. If production requirements change, you can increase capacity by bolting on longer carrying and bottom bars. However, before making this modification, waiting until you know your needs are growing is essential. This ensures your equipment is working at peak performance and maximizes energy efficiency.
Versatility
Plate heat exchangers are very versatile pieces of equipment. They’re used for heating and cooling, heat recovery, and evaporation for applications including dairy, food, and even heavy processes such as oil and power generation.
They’re also unsurpassed when dealing with liquids containing solids or fiber, which can clog other heat exchangers. In addition, many plate heat exchangers can be built modularly. If production needs change, you can expand your heat exchanger by bolting on longer carrying and bottom bars or adding additional plates. This is especially important for low-pressure fluids that require a high level of turbulence and velocity across the plates to minimize erosion and nozzle fouling.
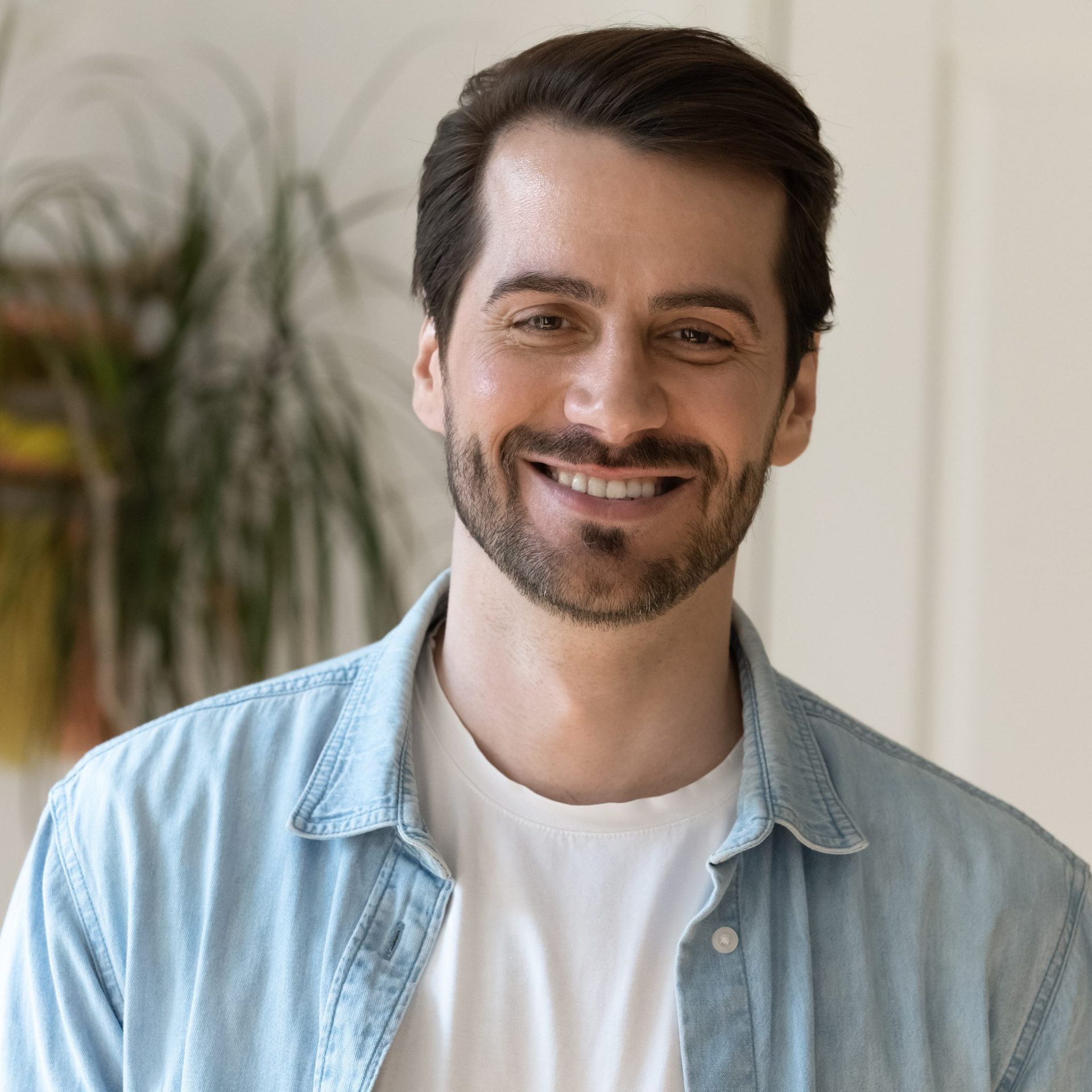
Jasper Bruxner is a passionate and versatile blogger with a keen eye for trends and a knack for crafting engaging content. As the founder of WendyWaldman, he has established himself as a trusted resource in a diverse range of niches, including food, tech, health, travel, business, lifestyle, and news. He tends to share the latest tech news, trends, and updates with the community built around Wendywaldman. His expertise and engaging writing style have attracted a loyal following, making him a respected voice in the online community.